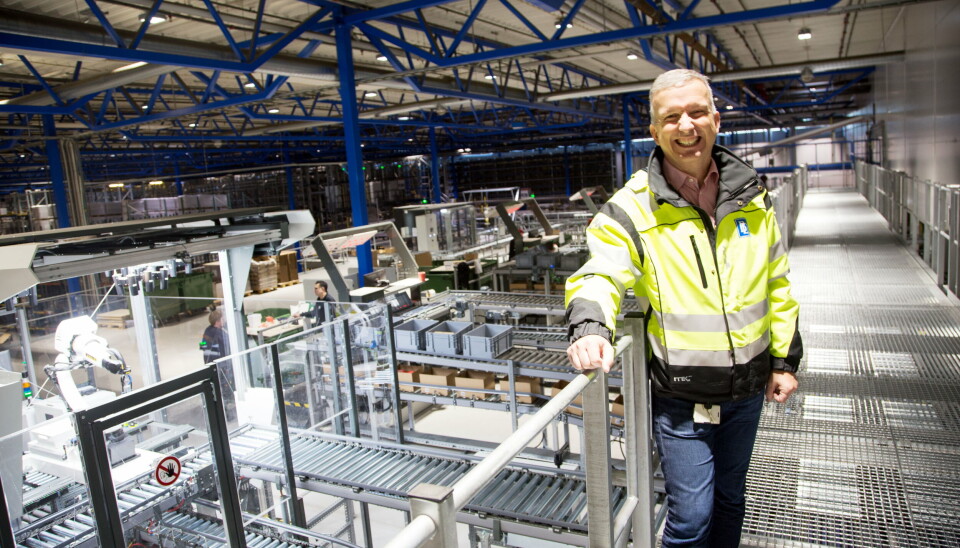
Stor investering gir store besparelser
LANGHUS: Det har vært en gigantisk investering. For Brødrene Dahl blir også innsparingen stor. Og den blir stadig større gjennom kunstig intelligens og maskinlæring.
Merk at denne artikkelen er over ett år gammel, og kan inneholde utdatert informasjon.
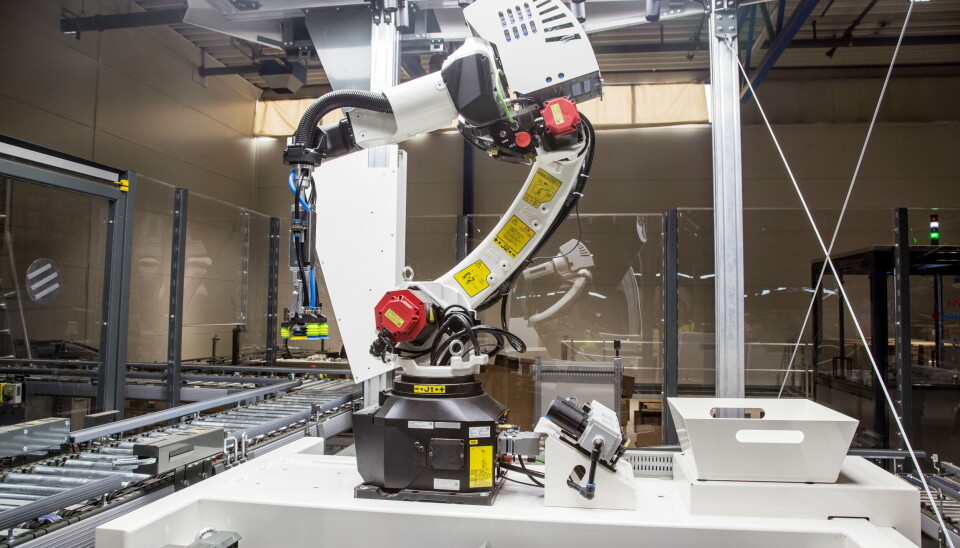
På Brødrene Dahls sentrallager på Langhus er det mer eller mindre hektisk aktivitet hele døgnet. I et 46.000 m² stort lager, på en tomt på totalt 110 mål, plukkes og sammenstilles ordre til kunder med høye krav i hele landet.
Totalt 280 ansatte sørger for at opptil 22.000 ordrelinjer fordeles korrekt på rundt 140 daglige transporter til hele landet. Til rett tid. For å gjøre driften så effektiv som mulig, er det gigantiske bygget full av en lang rekke ulike automasjonssystemer.
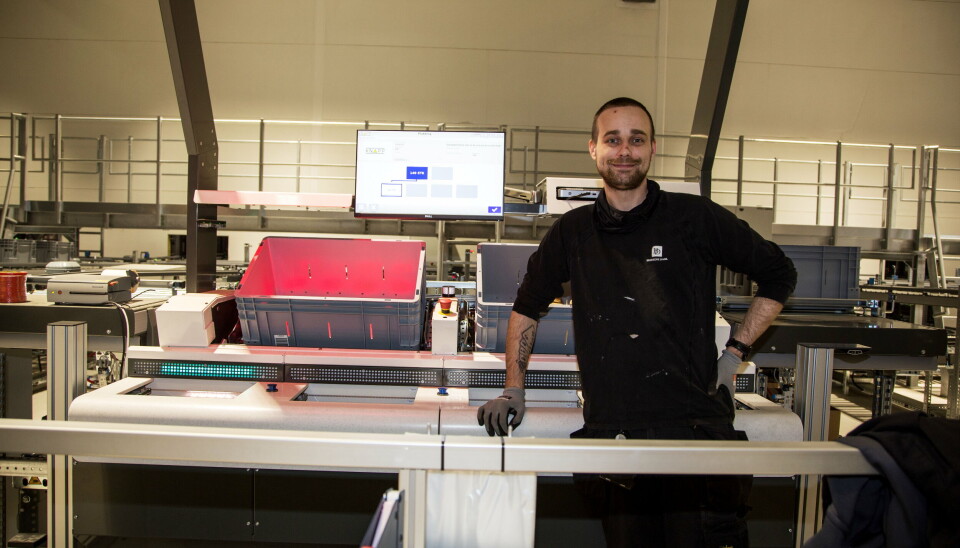
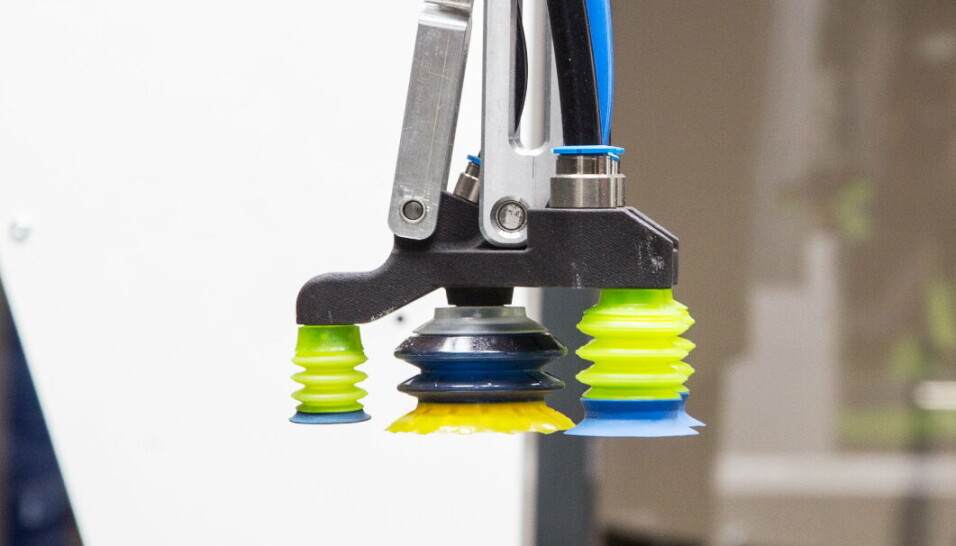
Her er pallekraner for paller i høytlager, automatisert rørlager, automatisert bufferlager, automatisert utgående sortering og lagerautomater. Lagerautomatene er imidlertid i ferd med å fases ut, etter den siste nyinvesteringen som ble satt i drift tidligere i høst: et skyttelanlegg for småvarer levert av østerrikske Knapp.
Sparer 32 årsverk
Tilknyttet skyttelanlegget på en nybygget mesanin står tre manuelle plukkstasjoner og en plukkrobot. Totalt kommer det nye skyttelanlegget til å sparre grossisten for 32 årsverk. Og de første månedene med drift har gått over all forventning forteller logistikkdirektør Ingar Bystrøm.
– Vi startet opp i september, og har ar ikke hatt noe større driftsavbrudd som har fått konsekvenser for kundene våre, sier Bystrøm.
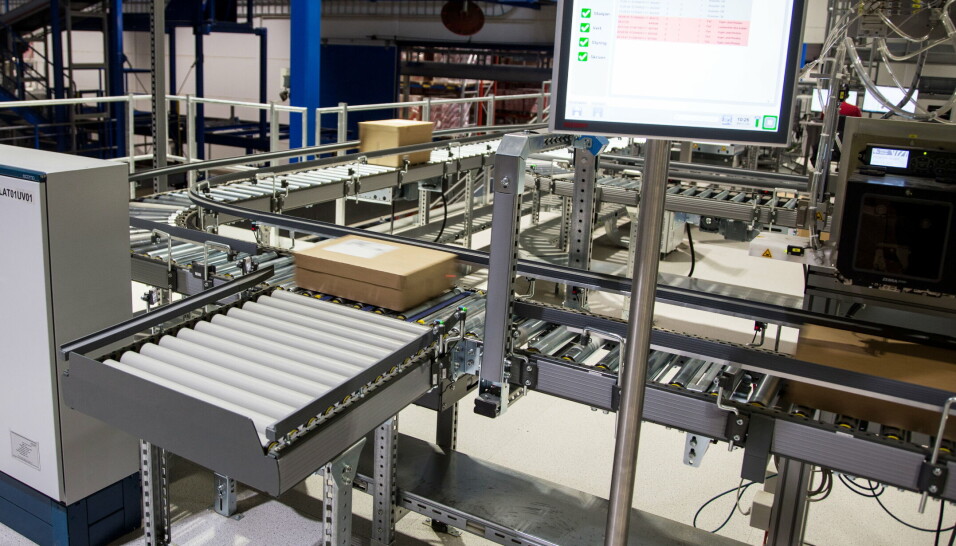
I prosessen med å velge hvilken type automatisk løsning Brødrene Dahl ville gå for når småvareplukket skulle automatiseres, ble de fleste typer løsninger vurdert.
– Det overordnede målet var å bedre produktiviteten vår. Vi gikk bredt ut og så på mange typer teknologi som kunne bedre effektiviteten. Vi tok utgangspunkt i behovene vi hadde og begrensningene som ligger her, nemlig at anlegget skulle inn i et eksisterende bygg. Det var også viktig å ta hensyn til at vi har døgnkontinuerlig drift og høye krav til avganger. Summen av dette gjorde at vår konklusjon var at et skyttelanlegg var riktig for oss, sier Bystrøm.
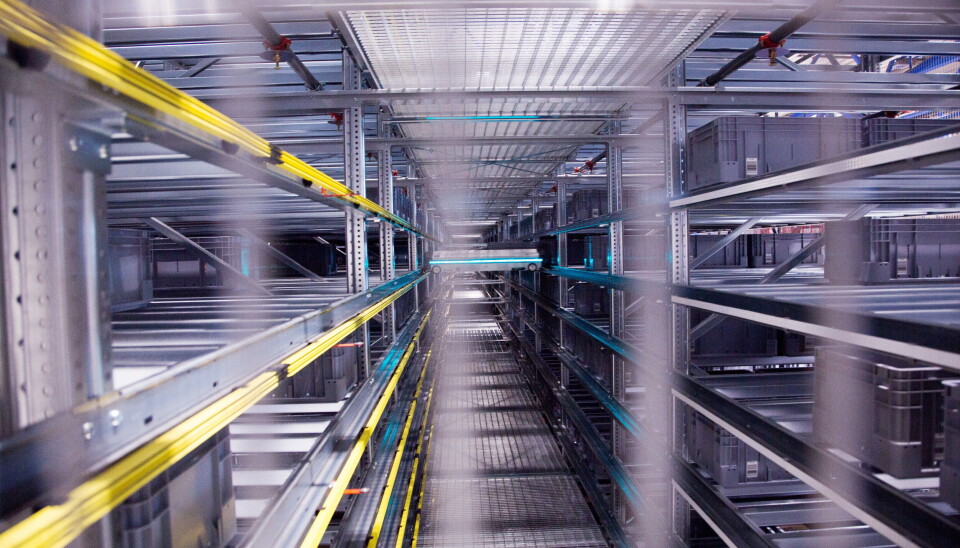
Totalt er det nå installert 36.000 kasser som 66 fireveis skytler utrettelig jobber med å hente frem til plukkstasjonene. Det er ved plukkstasjonene den virkelige effektiviseringen finner sted. Der mye av jobben tidligere var truck-kjøring og gåing, kommer nå kassene frem til stasjonene, der hver plukker kan pukke til fire samtidige kundeordre.
Enklere og raskere
Det lyser rødt i kassen det skal plukkes fra, antall enheter vises på en skjerm, og grønne ledlys viser hvor varene skal legges. I tillegg gjøres en kontrollveiing når plukket er gjort, som en kontroll på at rett vare og rett antall er plukket.
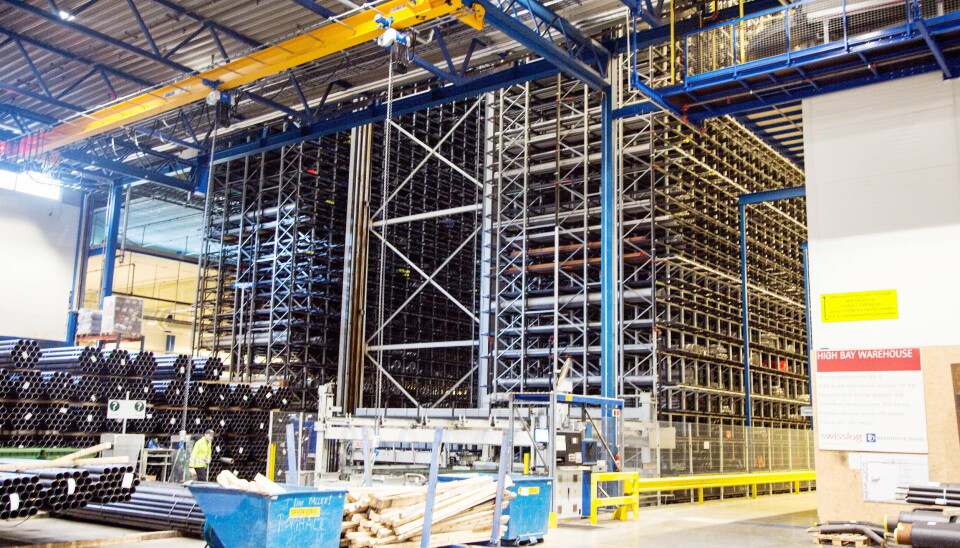
– Dette er mye enklere enn tidligere, og mye raskere. I tillegg er det omtrent umulig å gjøre feil – da gir systemet beskjed med en gang, sier Christian Myhre ved den ene plukkstasjonen, og viser hva som skjer om han legger for mye vekt ned i en eske. Da stopper systemet opp og krever korreksjon før Myhre kan plukke fra neste kasse.
I enden av rekken med plukkstasjoner står den mest fullautomatiserte løsningen. En plukkrobot med fire sugekopper på enden. Den skal etter hvert plukke så mange som mulig av ordrene. Den har noen styrker og noen svakheter sammenlignet med den menneskelige plukkeren.

– Om jeg skal plukke fem enheter av et produkt, kan et menneske ta alle i én bevegelse. Roboten må gjøre fem bevegelser. Så noen ting gjør mennesker bedre. Men effektiviteten til roboten ligger i at den kan plukke døgnet rundt, den trenger ikke ferie, pause eller er syk, sier logistikkdirektør Bystrøm.
Lærer gjennom AI-nettverk
Roboten har også sine klare begrensninger i hva den kan klare å plukke. Helt firkantede esker har ikke sugekoppene noen problemer med, men varer med litt annerledes utforming kan være vriene. Men roboten er lærevillig. Og også villig til å dele av sine erfaringer.
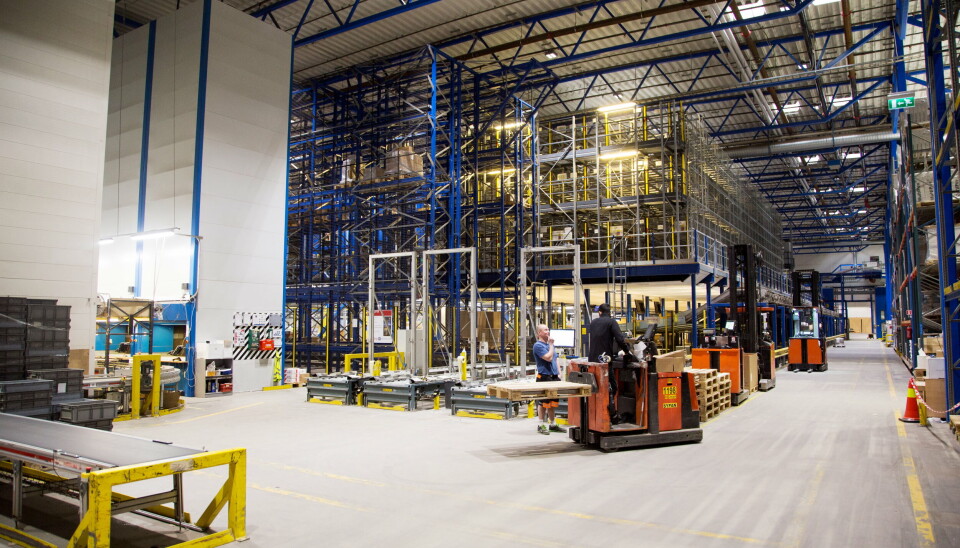
– Vi har programmert systemet slik at roboten får gjøre fem forsøk. Om den klarer det da, har den lært hvordan den skal gjøre det til neste gang. Dersom den ikke klarer det, går kassen videre til en av de manuelle stasjonene, forteller Bystrøm.
Fem feil gjør imidlertid ikke at roboten gir opp. Den har nemlig kompiser verden over som den kan lære av. Her kommer nettverksbasert kunstig intelligens og maskinlæring inn i bildet. Roboten på Langhus står nemlig koblet til et nettverk av tilsvarende roboter Knapp har levert andre steder i verden. Når en robot et eller annet sted plutselig finner ut hvordan den skal gripe en gitt gjenstand, vil den overføre kunnskapen til de andre robotene i nettverket.
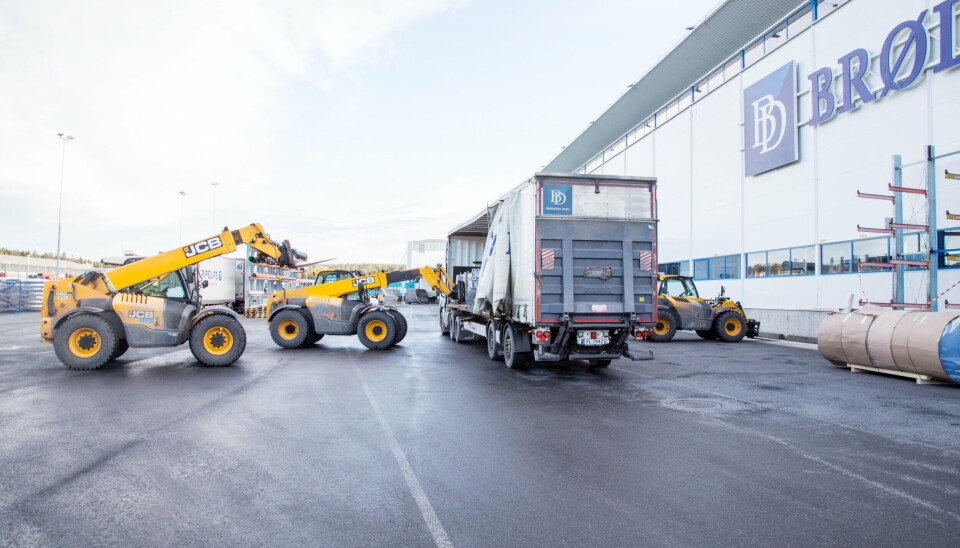
– Dermed vil roboten kunne plukke en større og større andel av varene i det automatiserte småvarelageret. Planen er å installere en slik robot til etter hvert også, sier Bystrøm.
- Ryddig prosess
Dette automatiserte småvarelageret og plukket skal altså ganske raskt spare Brødrene Dahl for rundt 32 årsverk. Det har Bystrøm tidlig forankret hos både ansatte og tillitsvalgte. Og ingen vil bli oppsagt som følge av effektiviseringen.
– Hele besparelsen ligger jo i sparte årsverk. Vi gikk tidlig inn i en dialog med de tillitsvalgte for å få en ryddig prosess. Det har gjort at vi besparelsene tas inn gjennom naturlig avgang og midlertidig kontrakter som går ut, slik at vi slipper å gå til en eneste ordinær oppsigelse, sier Bystrøm.
Investeringen i skyttelanlegget har kostet godt over 100 millioner kroner, men besparelsene er så store at Bystrøm forventer å oppnå en ROI på godt under fem år. Målet er at rundt 50 prosent av ordrelinjene og 45 prosent alle unike varer skal ligge i småvareanlegget.
I sentrallageret på Langhus er det som nevnt mange typer automasjon, levert av flere leverandører. Swisslog har for eksempel lever krananlegg til høytlageret, sampakkanlegg og samlebånd, mens Kasto har levert det automatiserte rørlageret. Nå kom også østerrikske Knapp inn. En stor utfordring er å få alle systemene til å snakke sammen og utfylle hverandre.
Astro har kontrollen
– De ulike automasjons leverandørene ne eier jo sin egen teknologi. Det er ikke nødvendigvis rett fram å få dem til å åpne teknologien for det som potensielt kan være en konkurrent. Her har vi hatt god nytte av Consafe som levere sitt Astro WMS til oss. Astro har overordnet regi på hele lageret, og styrer vareflyten, så tar hver enkelt løsning over og gjør de konkrete fysiske prosessene, forklarer Bystrøm.
– Consafe har vært en god samarbeidspartner i hele prosessen, og bidratt til å sikre god gjennomføring og godt sluttresultat, sier logistikkdirektøren.
Effektivisering er «the name of the game» for Bystrøm, som har nærmere 25 års fartstid i Brødrene Dahl. Selv om nytt skyttelanlegg er på plass, er det mange prosjekter under planlegging og underveis. Store og små.
– Vi gjør hele tiden tilpasninger i lageret. «Vi river en reol her og setter opp en reol der» for å gjøre driften på lageret mer effektiv, sier Bystrøm.
Sparer mange truck-kilometer
En stor besparelse som er underveis skjer på uteområdet, der 14 teleskoptrucker plukker store og ukurante varer. Som en del av storkonsernet Saint Gobain, fikk Brødrene Dahl tilgang på det franske konsernets ekspertise og datakraft.
– Vi har en betydelig produksjon også ute. På grunn av tomtens størrelse, kjører vi enormt mye med truck, og gjennom våre eiere har vi gjort en analyse av hele produksjonen på uteområdet. Det vi fant er at vi ved å flytte på plasseringen til rundt 200 varer, så sparer vi 540 km truckkjøring per måned. Det er viktig for miljøet og for kvaliteten i det vi gjør, sier Bystrøm.
Han er levende opptatt av å hele tiden finne nye gode løsninger, og ikke bli fanget av tidligere beslutninger.
– Jeg lærte noe viktig av en tidligere administrerende direktør i Brødrene Dahl: «Ikke tvihold på et dårlig valg». Jeg prøver å jobbe for en kultur der vi tør å prøve, og vi skal tørre å feile. Jeg vil mye heller teste ut tre forslag, hvor ett eller to feiler. Vi er under kontinuerlig utvikling, fordi markedet endrer seg, og fordi kundene og leverandørene endrer seg. Vi må tørre å gjøre feil underveis, så lenge vi lærer av feilene. Det å ha bygget opp en reol for seks måneder siden og så rive den i dag, ser ikke et nederlag for meg, så lenge vi forstår hvorfor valgene da og nå ble tatt. Og så lenge vi lærer av det.
Det neste litt større prosjektet for Brødrene Dahl på Langhus, er sannsynligvis å sette inn en liten armé av AGV-trucker på dagens manuelle linjer.